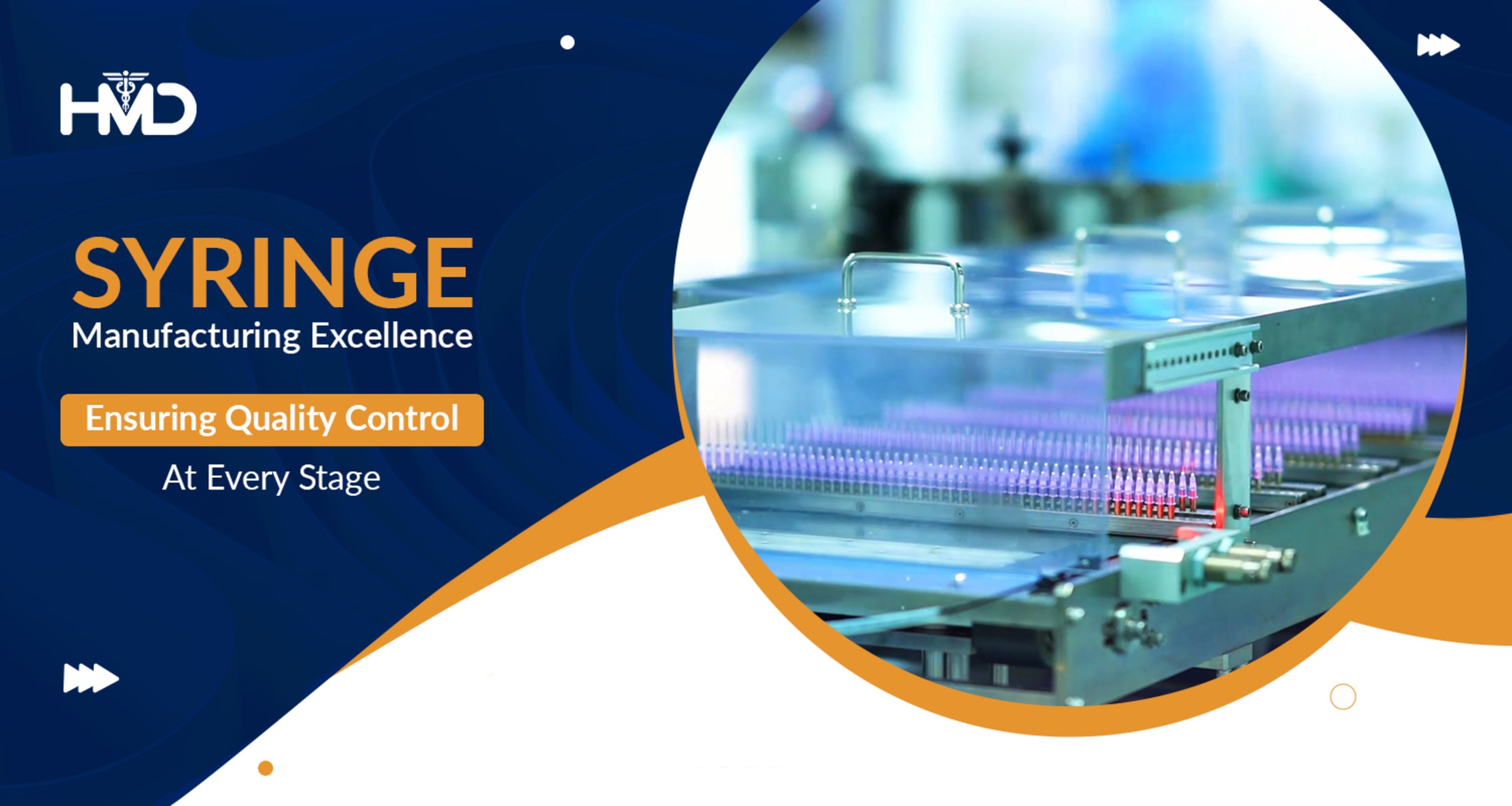
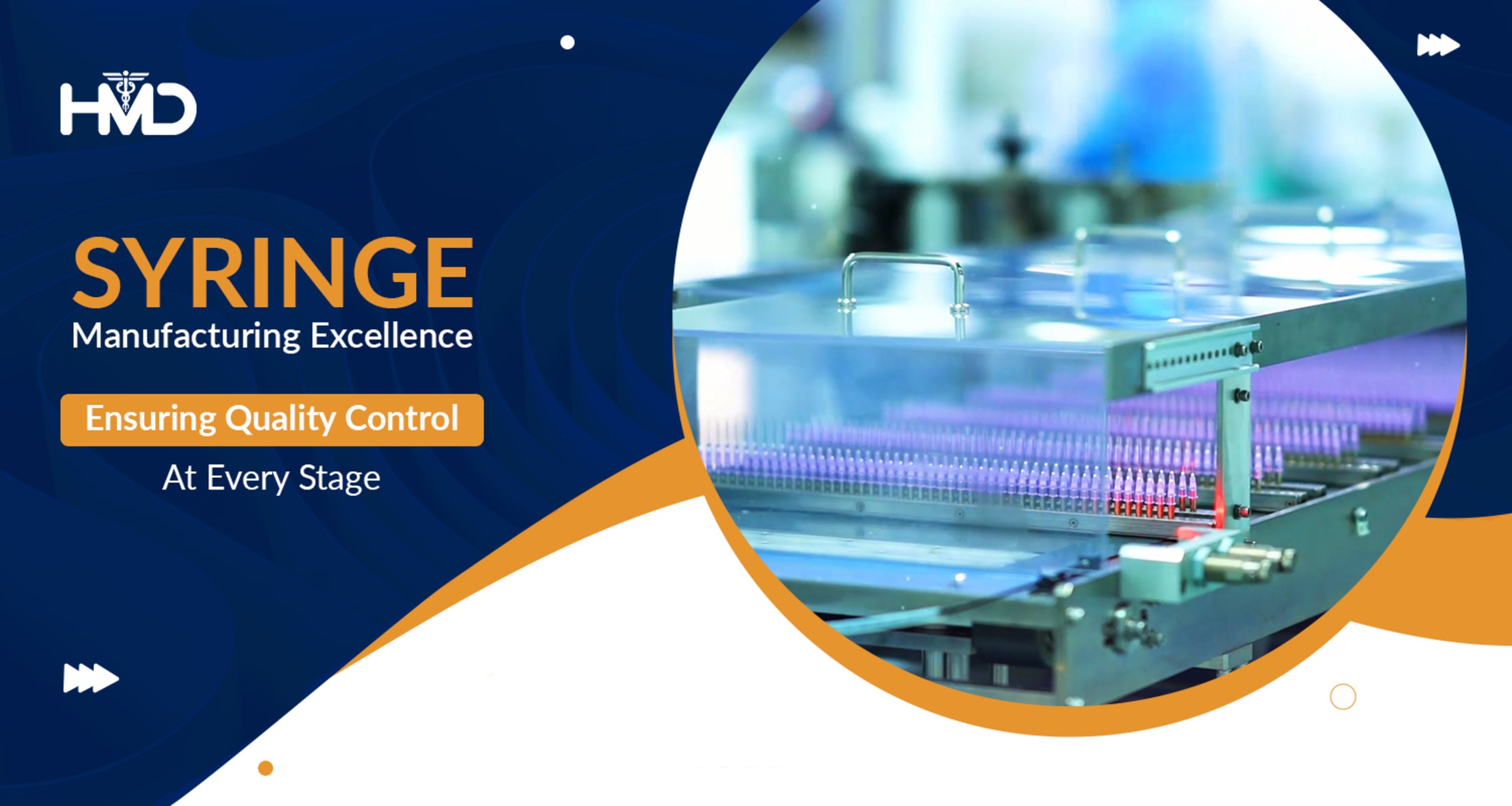
Syringes are fundamental tools in modern healthcare, serving essential functions such as drug administration and blood sampling. Their indispensability makes it imperative that every syringe adhere to the highest safety and efficiency standards. Quality control in syringe production is thus paramount, ensuring not only patient safety but also the effectiveness of medical treatments. Additionally, stringent quality checks are imperative to comply with regulatory standards.
This blog explores the intricate manufacturing process of syringes, which involves rigorous quality control measures that uphold their reliability and safety.
How are Syringes Manufactured?
Syringe manufacturing is a detailed process that begins with selecting high-quality, medical-grade materials. These materials, often plastics, are chosen for their durability, sterility, and compatibility with medical use. The production process involves precision moulding to form the barrel, plunger, and other components, ensuring each part meets exact size and shape specifications for optimal performance.
In the subsequent stages, these components are assembled in sterile environments to prevent contamination. The syringes are then equipped with needles, if necessary, and undergo a series of sterilization procedures. Throughout this process, adherence to industry safety and regulatory standards is paramount, ensuring each syringe produced is reliable and safe for medical applications.
Quality Control Measures
This involves a series of stringent checks and measures at each stage of production, adhering to the highest industry standards.
1. Raw Material Inspection: The quality check begins with thoroughly inspecting raw materials, ensuring they meet predefined standards for sterility and safety.
2. Dimensional Accuracy Checks: During production, syringes are checked for dimensional accuracy to match the specified sizes and volumes.
3. Sterility Testing: Post-manufacturing, syringes undergo rigorous sterility tests to ensure they are free from microbial contamination.
4. Functional Testing: This includes testing the plunger movement’s smoothness and the syringe barrel’s integrity.
5. Leak Test: Each syringe is tested for leaks to ensure it can hold and administer medication effectively.
6. Visual Inspection: Syringes are visually inspected for defects, such as cracks or misaligned parts.
7. Needle Sharpness Test: For syringes with needles, the sharpness and durability of the needle are tested to ensure efficient and pain-free penetration.
8. Lot Sampling: Random samples from production lots are tested to ensure consistency and adherence to quality standards across batches.
9. Packaging Integrity Check: The final product is checked for packaging integrity, ensuring it remains sterile and undamaged during transit and storage.
10. Regulatory Compliance: Regular audits and checks are conducted to ensure compliance with local and international regulatory standards, including the Food and Drug Administration (FDA).
These tests need not to be performed manually but some defects are also controlled by the automatic machine itself through vision inspection cameras. The quality inspection system acts as a double check to control product performance across high levels of mass manufacturing which is upheld as top regard by HMD.
Conclusion
The stringent quality checks and measures in syringe production are safeguards that ensure the highest standards of safety and efficacy. Regulatory compliance requirements guarantee that these standards are consistently met and upheld.
At HMD, we are committed to excellence. Each HMD syringe undergoes exhaustive quality control, ensuring it meets and surpasses the requisite quality and safety benchmarks. This dedication to rigorous testing means HMD syringes are designed for the utmost patient safety and care.